
Well I certainly know how to pick em.
Sustainability is a massive subject so I thought I would split it into sections. This week I wanted to look at what is sometimes the least acknowledged and worked upon element of sustainability.
When I was filling in countless forms to get on the Olympic park in 2012 as a supplier for the hospitality sponsor suites we had designed, one of the documents was on sustainability. I thought, like most suppliers who just wanted to get on and build stuff, what has this to do with me getting this job done.
On reading the document I was surprised and enlightened to find out that we as a company pretty much had it covered. We had been recycling in our workshops over 90% for years with our waste partner Wastercare.co.uk. We had been sourcing materials responsibly and from responsible suppliers, we had cut our use of acrylics favouring glass, we had a hire section to the business so built items didn't get wasted and we had a side hustle making 2D animal cut outs from off cuts for craft markets. What surprised me though, was the element that I hadn't thought about under the sustainability umbrella, but I had been doing ever since I had been in business as an employer, that is employment training and local community sustainability.
Both of my set companies have been based in very rural environments, not conjusive to rapid company growth. It meant we did not have the ease of access to the experienced event professionals needed, we had supply chain accessability issues and many communication and trucking issues. Employing suitable people was always the main issue, young rural workers we found were not used to long unusual hours, being away from home for weeks sometimes, missing family events etc. We went through many cycles of young and not so young people male and female, who just didn't like the industry and its many quirks.
However, we did strike gold many times.Its these successes that fall into our legacy of helping sustain communities and individuals whilst they work with us and beyond. I get a great deal of satisfaction to know people who have worked with us have moved on to be qualified, happy and successful in their own fields and the events industry. I see how they then pass that on by employing people of their own and provide job security where previously there wasn't the opportunity in the town.
So how did we do it? We always took an approach that our work wasn't complex but it had to be done certain ways to meet regulations and standards and the speed that our industry dictates. We always introduced new inexperienced team members in a standardised way. Their unofficial apprentice diary would look something like this:
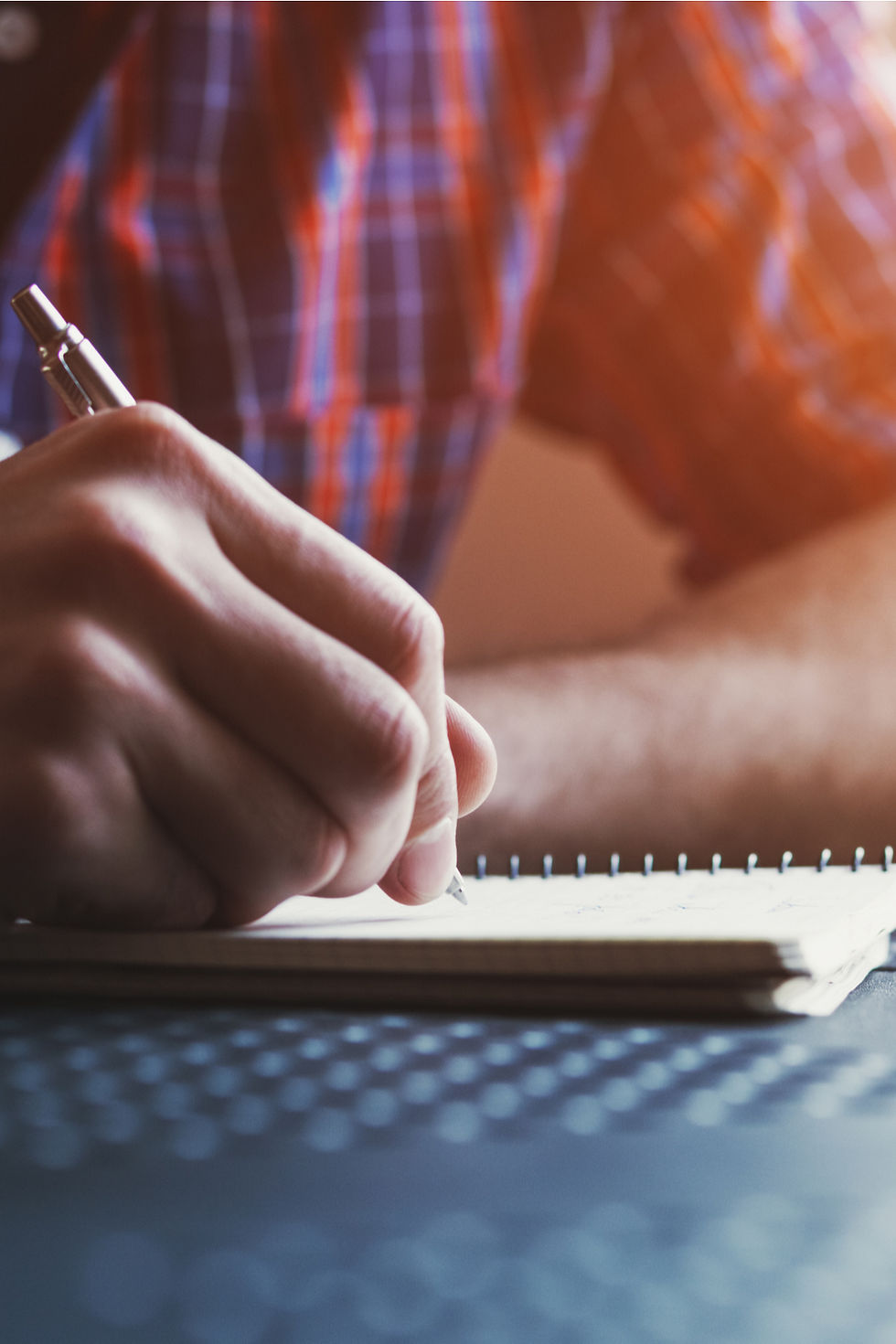
Day 1-7 -Spent all the time putting things back where they should be, tidying up and recycling, holding things for other people, putting the kettle on, HSE training and induction, cut my finger, loaded trucks.
Day 8-30 - Spent first month learning, how to make flats, wooden staging and putting site kits together , learnt what air tools are and how to use them, cut my finger! Trained on how to use other tools and machinery, loaded trucks.
Day 31 -180 Spent time learning new skills, haven't cut my finger, loaded and unloaded alot of trucks, stayed in a hotel and had beers I didn't pay for! Flew to (enter European city of choice)
Day 180 onwards , Keep learning new skills, learning CNC machine, bought my own tools, keep travelling in Europe, tired, want to see my family!!
When we had a team member who was going to stick it out, we, the management had had time together to see what their strengths were, we then encouraged them. We closely monitored what the company needed as well, but in the instance of one youngster, he trained for 3 years to be a qualified electrican and that work was useful for us as he developed and also now for him as he has his own company employing others in the same town. Some people may find it galling when you have trained someone at great cost, they bugger off when finished, but between our own contractural naievity and not wanting to stand in the way, who is to stop that sort of growth.
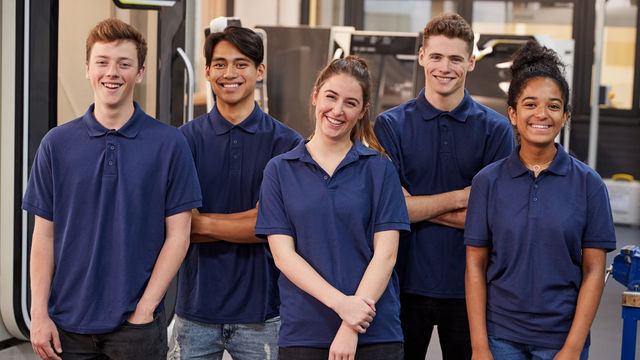
A lot of the larger set companies I have spoken to are struggling to find young employees, for the reasons aluded to above, because there has been a monumental shift to tech solutions but the industry still needs young blood coming through to work alongside this shift.
There are some entities working hard to help with training. The acredited Drama schools mostly run courses in production and stage management and experience is gained from working on the in house productions of the acting courses. In London i have come across one or two who have come thorugh this channel and of course Simon Whitaker the Stage One co founder, but it is mainly, mates bringing mates to work and giving it a go.
This is obviusoly not sustainable for the industry and whilst there are a maze of courses to go into management, they are harder to find for the specifics of the technical world and pretty much non existant for the carpentry/steel side. Certain elements of our industry have worked hard to get accreditation and recognition for their skills like Rigging which has changed dramatically over the last 20 years, but the scenic side is reliant on individual companies to train and guide our new generations into the event world using their own money or what is available from UK government apprentice schemes, although these are mainly pointed at construction models.
Lets herald those companies that are bringing new blood in and training them in house to be safer and more skilled workers. Lets herald the new employees who stick at it, the hours can be odeous, the conditions hard on site sometimes, the lengthy stints away from home and working for less than the technicians we work alongside can be irking, but, you do get to see some amazing things and experience life very differently at the coal face of major world events. There has to be a pay off!!
For me the pay off is seeing others succeed and I have a lovely list of those I have had the privelge to either mentor or help physically grow their skill base and career. If we can all do our bit we can help the wider community and economy and make our sometimes ridiculous looking industry look more more palatable for others to join.
So as we come out of this employment crisis in 2020 where lots of set companies had to let people go after lengthy furlough, I am asking are apprentices a cost effective way forward?
Let me know your thoughts and how your company develops people for our industry for the future.
Photos:Shutterstock
Σχόλια